
- PARAVIEW MICROSTRUCTURE SOFTWARE
- PARAVIEW MICROSTRUCTURE CODE
- PARAVIEW MICROSTRUCTURE DOWNLOAD
- PARAVIEW MICROSTRUCTURE FREE
PARAVIEW MICROSTRUCTURE FREE
Consequently, slip traces develop and are observed at the free surface of deformed specimens, with each slip trace associated with a local surface step. The authors should be contacted for further information on this in-house software.ĭuring mechanical loading, polycrystalline materials, such as the nickel-based superalloy investigated here, develop irreversible plastic deformation that can manifest in the formation of slip bands.
PARAVIEW MICROSTRUCTURE SOFTWARE
Digital image correlation were performed using the software Xcorrel HDIC. The second version was created with the software suite from Simmetrix (SimModeler Voxel), a commercially available software ( ).
PARAVIEW MICROSTRUCTURE CODE
One version of a mesh structure was created with XtalMesh 21, a publicly available code on GitHub ( ).
PARAVIEW MICROSTRUCTURE DOWNLOAD
The 3D voxelized dataset has been reconstructed using DREAM.3D, a software publicly available on GitHub ( ) or in the following link for direct download (. Reindexing of the EBSD data with the dictionary indexing approach was performed with EMsoft version 4.2, the latest version of the code is available at. The distortion correction algorithms and data analysis tools used in this study can be found at. Multi-modal datasets are of great interest for evaluating the dataset-merging procedures for distortion correction and for correlative measurements analysis tools. Multi-modal dataset of a polycrystalline metallic material: 3d microstructure and deformation fields. Two kinds of optimization variables, continuous and discrete variables, are adopted to describe the location of particles, and several numerical examples are carried out to provide insight into the optimal locations for different objectives. A genetic algorithm is employed to solve the inverse problem in which three parameters are proposed as optimization objective, including maximum peak force, maximum deformation at failure-point, and maximum fracture energy at failure-point. Hyperelasticity is used to model the rubber matrix and stiff inclusions, and the phase field method is used to model the fracture accounting for large deformation kinematics. In this paper, we study the optimal location of carbon black (CB) particle inclusions in a natural rubber (NR) matrix with the objective to maximize the rupture resistance of such polymer composites.
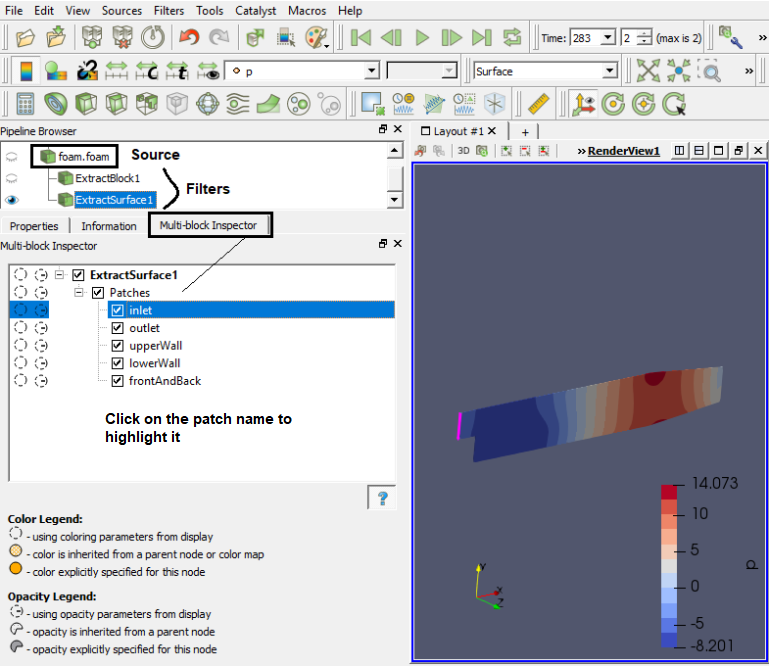
Optimization of material microstructure is strongly tied with the performance of composite materials at the macroscale and can be used to control desired macroscopic properties.
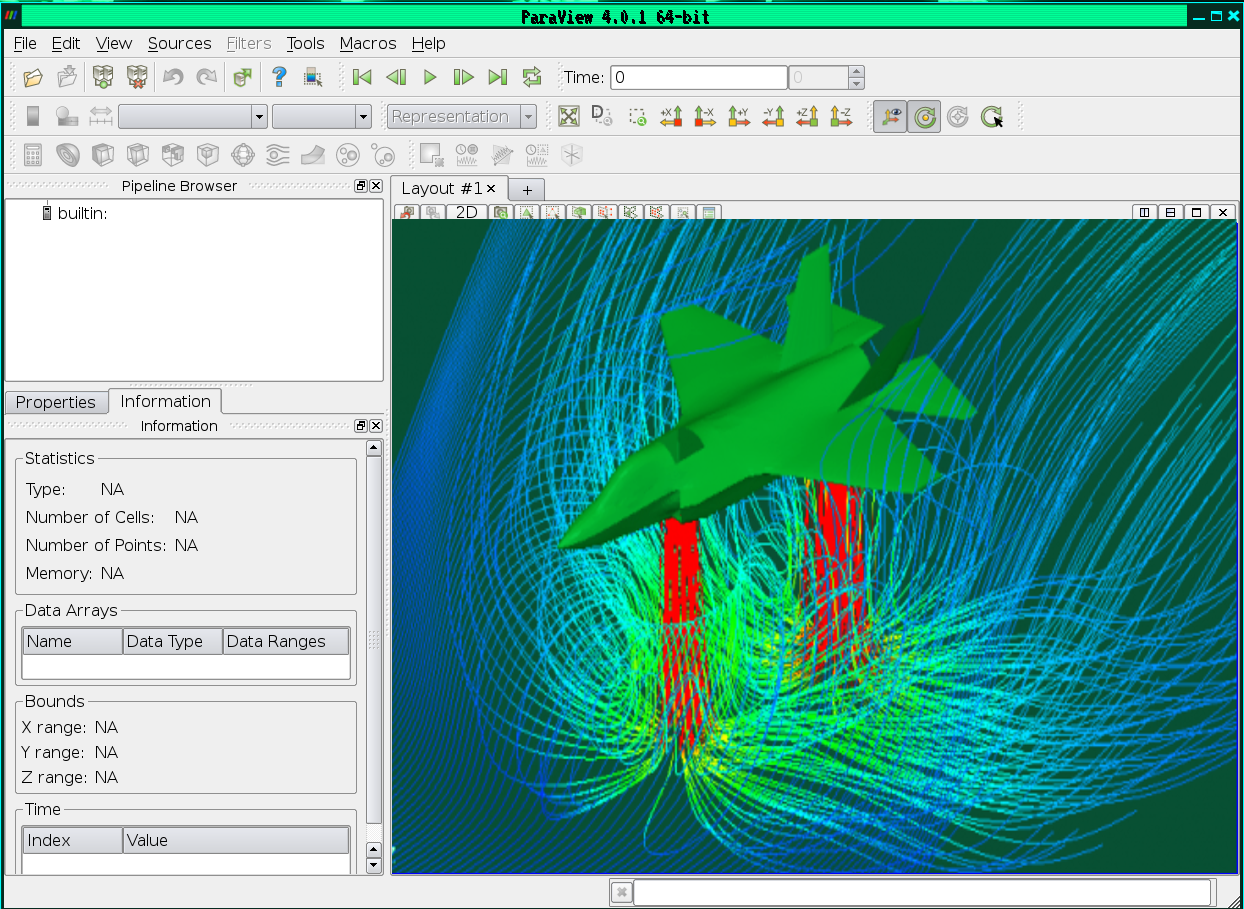
Journal of Verification, Validation and Uncertainty Quantification.Journal of Thermal Science and Engineering Applications.Journal of Offshore Mechanics and Arctic Engineering.Journal of Nuclear Engineering and Radiation Science.Journal of Nondestructive Evaluation, Diagnostics and Prognostics of Engineering Systems.Journal of Nanotechnology in Engineering and Medicine.Journal of Micro and Nano-Manufacturing.Journal of Manufacturing Science and Engineering.Journal of Engineering Materials and Technology.Journal of Engineering for Sustainable Buildings and Cities.
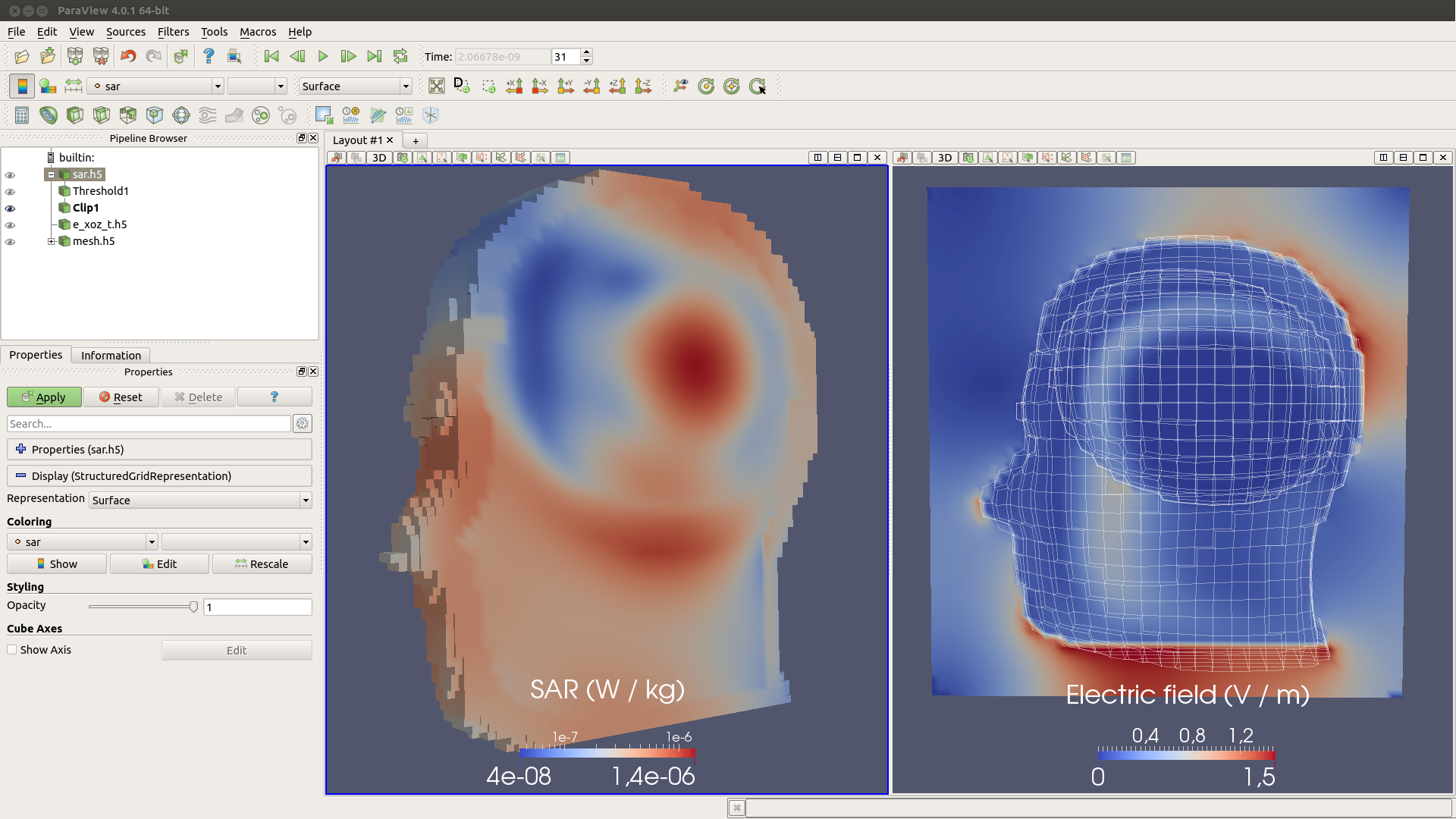
Journal of Engineering for Gas Turbines and Power.Journal of Engineering and Science in Medical Diagnostics and Therapy.Journal of Electrochemical Energy Conversion and Storage.

